High viscosity liquids can be difficult to process, and as a result, shell and tube or plate and frame Heat Exchangers can plug. To overcome this problem, Scraped Surface Heat Exchangers provide good mixing and enhanced heat transfer, therefore avoiding plugging. Spring-loaded Blades scrape the inner pipe wall promoting good heat transfer. Scraped Surface Heat Exchangers can operate from 190C to -30C.
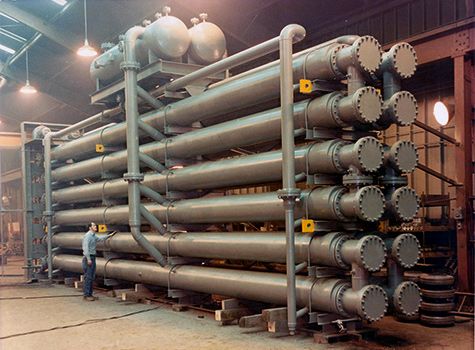
A continuous Scraped Surface Crystallizer is built as a double pipe element. The inner pipe ranges from 6″ NPS to 12″ NPS, and the outer pipe may be as big as 16″ NPS. The inner pipe contains spring-mounted scraping blades affixed to a centrally supported rotating shaft. These internals mix the process fluid that flows through the inner pipe while removing deposits that adhered to the inner pipe during cooling. The annulus between the inner and outer pipe contains counter or cocurrent flowing coolant.
SCRAPED SURFACE HEAT EXCHANGERS
Heat transfer occurs across the wall of the inner pipe as the coolant and the process fluid flow down the length of the crystallizer. As the process fluid cools, crystals form and adhere to the inner pipe wall, acting as a thermal resistance. The scraper blades rotate against the inner pipe wall and remove the crystals. The majority of crystal formation occurs in the bulk fluid: the small crystals scraped from the wall act as “seeds”, giving the desired product a favored location for crystal growth. The scraper blade generally rotates at 15 to 30 RPM to promote heat transfer that is consistent with good crystal growth and easy separation.
RELATED READING ABOUT SCRAPED SURFACE HEAT EXCHANGERS
- The Benefits of Vertical Bayonet VaporizersOur knowledge and expertise allow us to make the highest quality scraped surface heat exchangers and ammonia vaporizers.
- Three Critical Applications of Cryogenic Vaporizers
- Reasons to Choose Armstrong Chemtec Chlorine Vaporizers